Thermal Energy Efficiency Upgrade at Aurivo Dairy Ingredients
Aurivo Dairy Ingredients, a milk processing plant with a significant thermal demand, reinvent the supply of thermal energy to the process through the EXEED scheme.
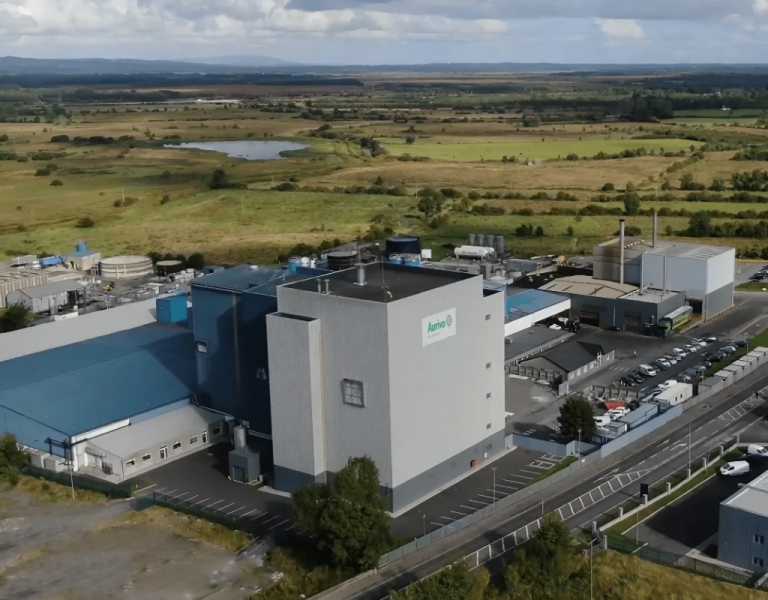
The Aurivo Dairy Ingredients business is based in Ballaghaderreen, Co. Roscommon. The business produces c. 60,000 tons of dairy products such as enriched milk powders, (EMP), fat filled milk powders (FFMP), yoghurt powders, with 2 No. spray dryers and over 10,000 tons of butter annually. The powder is mainly for export while the butter is produced for consumption within Ireland under the Connacht Gold brand.
Key achievements
11% reduction in energy bills
7.7% decrease in site energy consumption
51 opportunities for improvement were identified during the Challenge and Analyse Exercise
The project
As a large energy user, Aurivo was seeking new methods to reduce their carbon emissions and energy costs at the Ballaghaderreen site. They applied for the EXEED grant - SEAI's programme 'Excellence in Energy Efficiency Design'. This is for organisations who are planning an energy investment project and SEAI provide up to €3,000,000 in grant support per project.
Through the EXEED Stage 1 process, they carried out a review of the thermal heating systems. The aim of this was to identify opportunities that could form an optimisation programme for the thermal system with the dual aim of improving the thermal performance of the system while simplifying and futureproofing the distribution network site.
There was a significant increase in both management and operator knowledge of the whole steam system through the engagement of personnel in the challenge and analyse exercises, which are steps in Stage 1 of EXEED. These were carried out to identify the 51 opportunities for improvement and through the delivery of advanced boiler and steam training.
Energy efficiency design
Through the implementation of a different EXEED project in Aurivo's milk bottling plant in Donegal, the company experienced the benefits of the Energy Efficiency Design [EED] approach first-hand. This inspired the team to complete the Ballaghaderreen project using the same methodology.
The project focused on all elements of the thermal system from end user through to generation as per the Energy Venn Diagram [EVD], which is a component of the Energy Efficient Design Management approach. It highlights that understanding the criteria affecting the energy efficiency of thermal systems requires a holistic approach to projects.
Measures implemented include:
- Improving the distribution system in order to reduce heat loss through upgrade insulation and steam trapping
- Upgrading the condensate and boiler feedwater systems to maximise the amount of condensate return volume and temperature to include:
- Replacement of the current Heavy Fuel Oil boiler with two 14tph LNG fired steam boilers with dual fuel capability - gas and light fuel oil
- Installation of state-of-the-art metering and monitoring of the thermal system.
- Remediation of the dryer condensate system including automation of the heat recovery system to ensure maximum use of thermal energy recovery.
This has enhanced management's understanding of the operational control requirements of the thermal system, which is one of their largest operational costs on site.
Results
As a result of this project, Aurivo have experienced annual cost saving of €750,000, which translates into 13.8 GWh of thermal energy savings per year. The total project cost was approx. €3million and SEAI provided a grant of €1million through the EXEED grant programme.
"I would highly recommend the EXEED process to any company that is making significant investment in energy intensive plant and equipment. We have been using the energy efficient design principle for several years and the benefits that are delivered through the process will be seen for years to come on our site."
What's next?
Aurivo have been working on further energy efficiency and decarbonisation initiatives throughout the site to complement the impressive list of achievements completed to date. This includes the installation of:
- a biomass boiler
- state of the art dryer
- liquefied natural gas (LNG) replacement for heavy fuel oil (HFO)
and year on year energy efficiency improvements under the ISO50001 certified energy management system.
The decarbonisation plan has ambitions to achieve net carbon zero in this energy intensive manufacturing process with a suite of efficiency projects, technology changes and further fuel switching options as the technologies evolve in the next 10 years.
The success of the EXEED process has now been recognised and will be a prerequisite for large capital expenditure projects as part of the approvals process.
Read more about EXEED